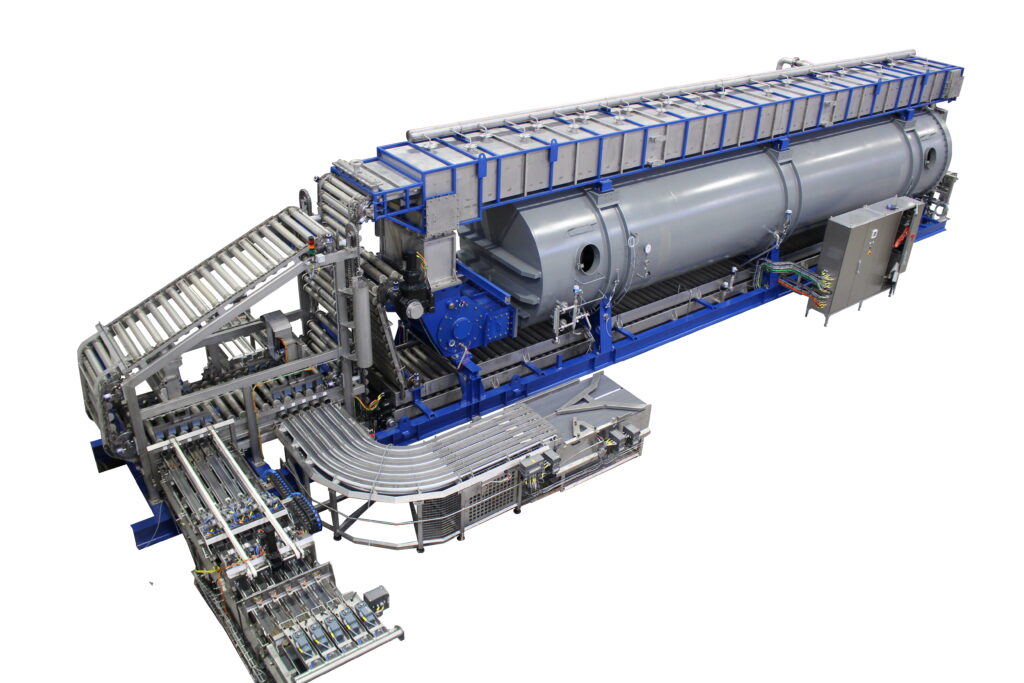
There are multiple solutions available to meet food sterilization requirements. Both Batch Retort and Continuous Retort systems offer mature, well proven methods for this application. So why choose a Continuous Retort process?
Sterilization is critical for a significant amount of the food we humans consume or feed to our trusted pet companions. Sterilization time and temperature is designed to extend product shelf life and to neutralize Clostridium botulinum, a potent bacterium that can cause death in humans and animals.
Thermal Process Advantage
With a Continuous Retort, interior containers are not nested between outer containers, eliminating the container master-slave heat transfer relationship common to Batch Retort processing. The STOCK Hydrolock Continuous Retort integrated loader forms a single file array of containers that enter the sterilization chamber in a non-nested format, allowing instantaneous heat penetration to each individual container.
Unlike the Batch Retort, a Continuous Retort requires no Come Up time. Come Up time is defined as the time it takes all points of the sterilizer to be equal to or greater than the filed process temperature. By eliminating differential temperature seen by the nested load of a Batch Retort, the STOCK Hydrolock Continuous Retort provides a shorter, more uniform thermal process.
Energy Efficiency
In comparison, a Continuous Retort provides better energy efficiency over an equivalent Batch Retort system.
The STOCK Hydrolock Continuous Retort can be held at process temperature for as long as there is a need for production. Unlike a Batch Retort, the Continuous Retort requires no cycling between Come Up, Sterilize and Cooling. These process phases are maintained in a steady state control loop with indirect heat exchangers, eliminating high demand energy usage needed to heat and cool the metal of the shell.
Layout Consideration
A Continuous Retort requires less floorspace than the equivalent Batch Retort system.
The STOCK Hydrolock Continuous Retort not only includes the shell for the sterilization process, a fully integrated loading and unloading system is also included within a single frame. This consolidates overall footprint and facilitates ease of installation.
Batch Retort applications not only require multiple shells for the sterilization process to achieve the same volume as a Continuous Retort, but the Batch Retort system also requires multiple pieces of equipment for container handling including sperate loader, shuttle, unloader, and basket transfer conveyance.
Flexibility and Maintenance
Both the Continuous Retort and Batch Retort offer flexibility when it comes to the types of packaging and products that can be handled and sterilized. This includes metal cans, glass, pouches, and plastic trays, as well as others.
A Continuous Retort is usually designed around a specific set of container geometries and has the most benefit in high volume applications. Batch Retort systems can generally process any container geometry but may require sperate material handling systems for each.
A Continuous Retort requires less maintenance, fewer replacement parts, and less labor to operate than the equivalent Batch Retort system.
Conclusion
The STOCK Hydrolock Continuous Retort is a great fit when your needs are focused on high volume processing in a dedicated set of similar container geometries and your desire is to be as energy efficient as possible, with minimal operational labor, and lower cost of overall maintenance.
If your requirements demand the need for an array of different container geometries and product processing, the flexibility of a STOCK Batch Retort system may be a better fit.
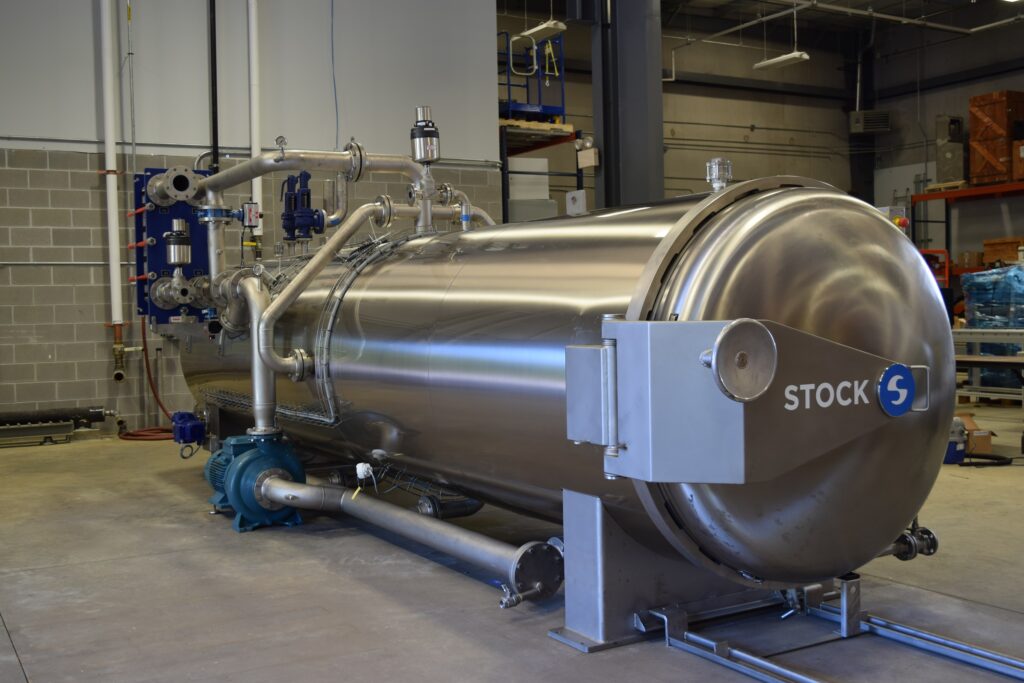