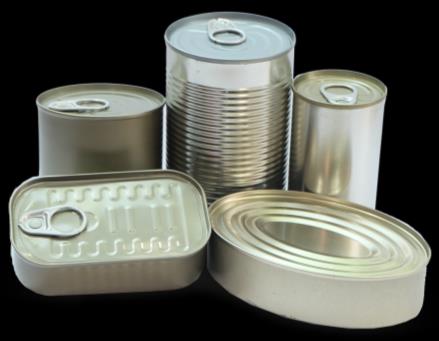
Preserving food in cans was introduced in the early 1800’s. The technology is so mature that consumers today can purchase a pressure cooker to preserve their own products. A saturated steam process is basically a very large pressure cooker typically ranging in diameter from 1300mm-1800mm (52”-72”) with lengths that can exceed 12 meters (40’). When applicable, the saturated steam retort is the simplest and least expensive retort to build, but it is limited on the types of containers that will work due to its inability to use overpressure during the heating phases of the batch. The product range for saturated steam processes involves canned products that do not require agitation (defined as a “Static” or “Still” process) including vegetables, canned proteins (chicken, pork, beef, seafood), and petfood.
Horizontal Saturated Steam Retort
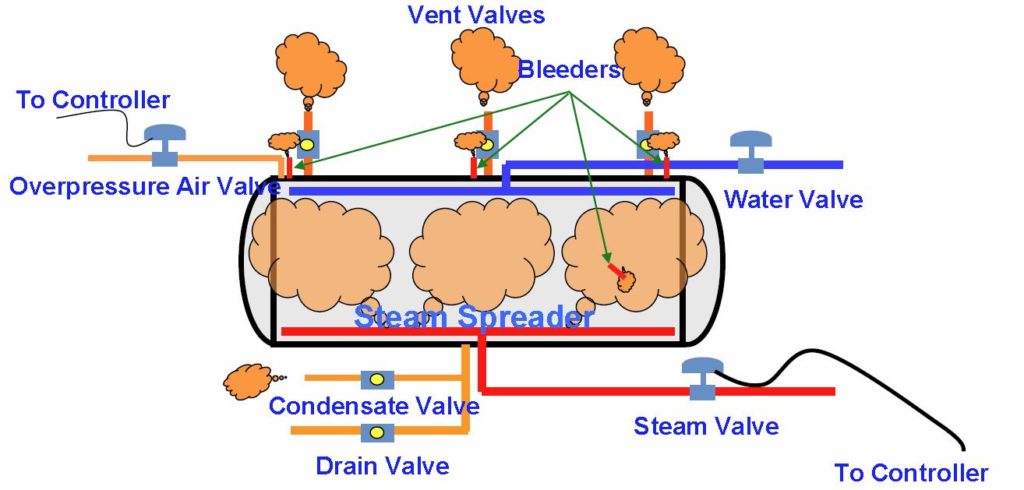
Saturated Steam Vent/Bleeders
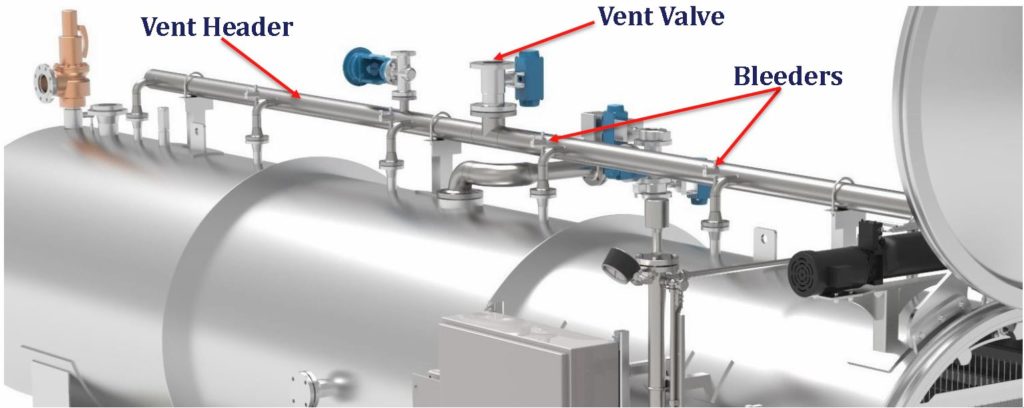
- Retort Vent – The first step in a steam process is “come-up vent open”. The purpose of the vent is to eliminate air from the retort. 70-80% of the space in the retort is occupied by air with the product loaded inside. The vent step is a critical process step that requires a heat distribution study to determine the time and temperature of the vent schedule. The results of the study are part of the filed thermal process with FDA/USDA. The vent valve is commonly located along the top of the retort and requires a switch on the valve to confirm that the vent did open.
- Retort Bleeders – The bleeders are relatively small (typically .25”) orifices strategically placed on the retort to eliminate any residual air left in the retort after the vent phase is complete. The retort operator is required to visually confirm that the bleeders are expelling steam as part of their operator entries during the process. The bleeders remain open until the retort enters the cooling phase. Retort bleeders are typically placed above the center of each basket and one at the instrument cluster (location of the temperature measuring devices). In addition to driving out residual air, the bleeders also put a load on the steam valve which helps maintain steam flow and helps heat distribution.
- Vent Valve – During the come-up vent open step the vent valve is opened. It is critical that the vent valve is a full-bore valve that is 100% open to allow thw free flow of steam out of the retort. The vent valve is commonly located along the top of the retort and requires a switch on the valve to confirm that the vent did open.
- Air Elimination – In a steam retort, remember the first step is Come-Up Vent Open. In this step, Steam in introduced in the retort in order to chase the air in the vessel out of the top of the retort. Air inside of a steam process acts as an insulator and cerates cold spots in the retort. If air remains in the retort, products will be under-processed.
- Heat Distribution Vent Studies – Due to the importance surrounding air elimination, thermocouples are strategically placed in the retort and a vent study is executed to observe and document when the temperature probe readings converge and therefore validate that air is void. Also monitoring the steam table temperature/pressure correlation helps validate that the air is eliminated. Data collected from the vent study creates a vent schedule for the retort that is filed with the FDA/USDA. Any changes to the vent header piping requires the plant to re-run the heat distribution study and reset the vent schedule.
- The Vent Discharge Header – Another critical factor of the vent step is to ensure that while venting, no back-pressure is being created due to any flow restrictions in the vent header that expels steam to the atmosphere. It is critical that the vent discharge piping (Vent Header) have a cross-sectional area larger than the pipes feeding it from the retorts.
Saturated Steam Process Instrumentation
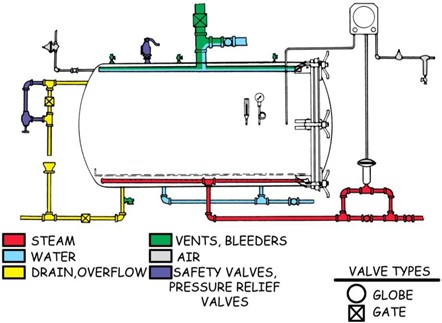
- Chart Recorder – An instrument that measures and records internal retort critical factors as part of the process recordkeeping mandated by FDA/USDA. For a steam process, Temperature and Pressure are typically recorded. A new chart is replaced every 24 hours.
- Pressure Transmitter – Certified Pressure Reference Gauge to measure vessel pressure is required. The transmitter is also certified at a minimum annually.
- Temperature Control RTD – A temperature probe that the PLC uses to control the retort heating profile.
- Certified Temperature Indicator – Certified temperature reference thermometer is required. The device can be a mercury in glass thermometer or an approved digital thermometer certified for accuracy at a minimum annually. The Chart Recorder and Temperature Control RTD are calibrated to the reference thermometer.
- Steam Spreader – As steam is applied to the retort, it is critical that the steam be distributed evenly along the length of the vessel. Since heat naturally rises, the steam spreaders are located along the bottom of the retort so that as the steam rises, the product will draw the heat from the steam effectively. Steam pipes are installed at the bottom of the retort and holes are strategically drilled along the steam spreader pipe. The number and diameter of the holes, and the position of the holes are defined in the federal code of regulations 21CFR Part 113.40 and the hole design is recorded in the filed thermal process with FDA/USDA as a critical factor.
- Condensate Valve – A steam process develops large amount of condensate (hot water) as the steam heats the product (the steam turns back into a liquid as the product draws the out the heat). This condensate will collect in the bottom and cover the steam spreader and product which would cause under-processed product. To eliminate this risk, a condensate valve is used to drain out the water and an instrument that detect level is installed to monitor the level during the heating phases of the process.
- Steam Control Valve – To control the heat in a steam process, a special valve is required to maintain a tight temperature profile during the heating phases of the process. Called a control valve it provides steam to the retort with a linear flow anywhere between 0-100% compared to a standard valve that is either 100% open or 100% closed. This provides temperature control with .5 degrees Fahrenheit inside the retort shell to meet regulatory requirements.
- Air Overpressure Control Valve – Introduction of air overpressure in a steam process is only allowable during the cooling steps. At the beginning of cooling, water is introduced to the retort. The water creates a rapid collapse of the steam (the temperature drops along with the corresponding pressure) and the corresponding pressure drop creates a vacuum. This would greatly stress the hermetic container seals, so to combat the problem, air is added to the retort to stabilize the pressure when the steam collapses. Like the Steam control valve, the Air Overpressure control valve can operate between 0-100% of its flow.
Steam Retort Container Loading
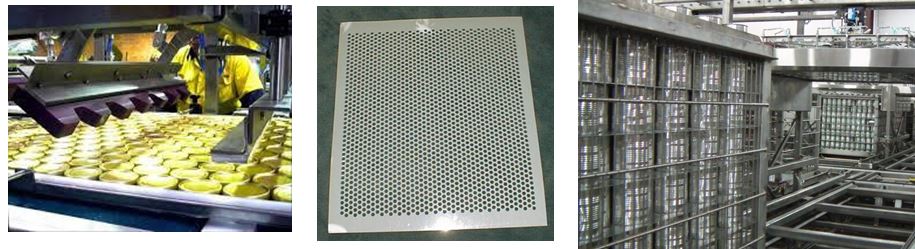
Packing Method and Product Orientation – Products (typically cans) are strategically placed in a basket with perforated divider-sheets also known as slip-sheets in between each layer. Cans swept in the basket create a staggered pattern of cans that provides channels for the steam to pass through easily and distribute heat to the entire load. It is important that the baskets and divider-sheets are designed to maximize open area. These baskets/loaded patterns/divider-sheets are tested during the heat distribution (HD) studies and the results are filed with the FDA/USDA. Any changes to these components can cause significant under-processed product. Any changes to these critical factors requires that the HD studies be re-validated.
Steam Retort Critical Operator Entries
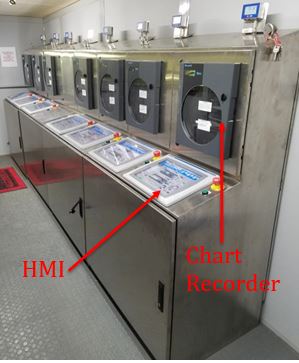
There are multiple entries that an operator makes during every batch process of critical factors per FDA/USDA requirements. In the event that an entry is outside of the parameters of the filed thermal process with FDA/USDA, a process deviation is created on the record and requires clearance by the plant’s process authority. The product may be cleared, put on hold for further evaluation, or destroyed. Below are minimal entries required for a steam process with automated PLC control. Some plant may have additional protocols that are required. For manual systems, many more entries are required such as time of each step of the process by reading a timer. For automated systems, a batch record is generated with all times, readings and entries recoded.
Initial Temperature (I.T.) – Measures the coldest container prior to starting the process. The operator will take a physical reading with a thermometer and make an entry when prompted by the HMI (Human Machine Interface).
Temperature Reference Thermometer – The operator will be prompted during the process to take readings of the certified temperature reference thermometer.
Chart Recorder Reading – The operator will be prompted during the process to take a
reading of the Chart Recorder temperature.
Bleeders – The operator will be prompted during the process to ensure that the bleeders are expelling steam at all locations.